Hydrostatic Testing: The Pressure-Proof Way to Guarantee Cylinder Safety
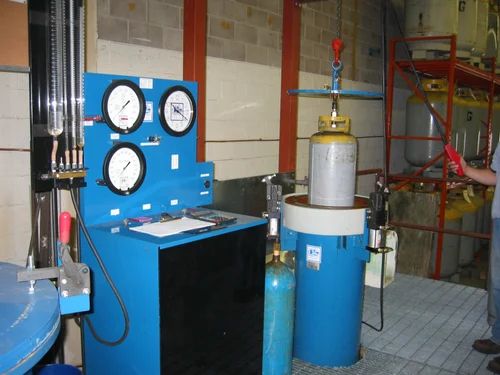
Introduction
Compressed-gas cylinders are the silent workhorses of countless industries—fire protection, SCUBA, aviation, medical oxygen, and industrial welding all rely on vessels that hold gas at immense pressures. Over time, heat, vibration, corrosion, and simple metal fatigue can weaken those shells. If a cylinder fails without warning, the result can be catastrophic. That is why hydrostatic testing is mandatory: it verifies that a container can still withstand its rated pressure plus a hefty safety margin.
What Is Hydrostatic Testing?
In its simplest form, hydrostatic testing is a nondestructive pressure test that fills the cylinder with water (which is nearly incompressible) and then pressurizes it well above its normal operating level. Technicians measure how much the shell expands under load and how much of that expansion is permanent once the pressure is released. Excess “permanent set” means the metal has yielded and the vessel is no longer safe for service.
The method is preferred over pneumatic tests because water stores minimal energy even at high pressure, reducing the danger of an explosion should the cylinder rupture.
Key Reasons the Test Matters
- Life Safety – A rupturing 3,000-psi SCBA bottle can unleash force comparable to a small bomb. Confirming structural integrity protects both users and bystanders.
- Regulatory Compliance – Agencies such as the U.S. Department of Transportation (DOT) and Transport Canada require periodic hydro tests as a condition of cylinder re-qualification.
- Insurance & Liability – In the event of an accident, proof of current test dates can limit legal exposure and keep insurance policies valid.
- Cost Control – Requalifying a cylinder is far cheaper than buying a new one; catching corrosion early can extend service life by years.
Governing Codes and Standards
- 49 CFR Part 180 (United States) specifies test intervals—typically every five years for most high-pressure cylinders, but up to 12 years for certain fire extinguishers bearing a star stamp.
- ISO 7866 and ISO 18119 outline international requirements for seamless aluminum and composite cylinders.
- NFPA 10 assigns hydrostatic schedules to portable fire extinguishers: CO₂ tanks every five years, dry-chemical steel shells every 12 years.
- CG-A (Compressed Gas Association) Pamphlet C-1 details acceptable testing apparatus, expansion-measuring devices, and calibration protocols.
Where Hydrostatic Testing Applies
Industry | Typical Cylinder Type | Test Interval | Special Notes |
Fire Protection | Steel dry-chemical, CO₂, clean-agent | 5–12 years | Tagging must match NFPA 10 |
SCBA / Firefighter Air Packs | Carbon-fiber composite | 5 years (15-year service life) | End-of-life date cannot be extended |
Medical Oxygen | Aluminum or steel | 5 years | Must meet FDA cleanliness |
SCUBA Diving | Steel or aluminum tanks | 5 years (U.S.) | Visual inspection also required annually |
Industrial Gases | High-pressure steel | 5 years | Some specialty gases need more frequent tests |
Step-by-Step Process
- Pre-Test Inspection – Technicians remove the valve, examine threads, and look for dents, gouges, or corrosion. Cylinders failing visual inspection are condemned immediately.
- Water Fill & Air Removal – The vessel is filled with temperature-controlled water and placed inside a sealed steel jacket. All trapped air is purged to prevent false readings.
- Pressurization – A hydraulic pump raises internal pressure to 1.5 times the cylinder’s service rating (e.g., 7,500 psi for a 5,000 psi SCBA bottle).
- Expansion Measurement – Gauges record total expansion and compare it with the cylinder’s elastic expansion. Excess permanent expansion—usually more than 10 % of total—is grounds for rejection.
- Pressure Release & Drain – Pressure is slowly vented, water is drained, and the shell is dried to prevent internal rust.
- Stamping & Documentation – Passing cylinders receive a new retest date stamp or label plus a record in the facility’s permanent log. Failures are punctured or cut to prevent reuse.
Common Causes of Failure
- Internal Rust Pitting from moisture left in partially emptied cylinders
- Galvanic Corrosion where dissimilar metals meet (valve-to-neck interface)
- Over-Pressurization due to faulty regulators or relief devices
- Heat Damage that changes metal temper, often invisible externally
- Thread Damage leading to poor valve seating and stress concentrations
Selecting a Qualified Testing Facility
Because a flawed test can be as dangerous as no test, always verify:
Checklist Item | Why It Matters |
DOT-Registered Requalifier Number | Ensures the lab meets federal standards |
Calibration Certificates | Confirms equipment accuracy within legal tolerances |
Digital Expansion Data | Provides a permanent, tamper-proof record |
Valve Rebuilding Capability | Speeds turnaround and guarantees proper torque |
Liability Insurance | Protects your organization while cylinders are off-site |
For companies seeking a proven partner, hydrostatic testing from Service-d Fire Equipment offers DOT-licensed facilities, same-day turnaround on many extinguisher types, and electronic reports that integrate with asset-management systems.
Best Practices for Cylinder Owners
- Track Dates Proactively – Use barcode or RFID tagging to alert staff 60 days before a cylinder’s retest deadline.
- Control Moisture – Keep partially used cylinders pressurized to at least 25 % of rating; never leave them empty with the valve open.
- Standardize Inventory – Fewer cylinder models mean fewer test schedules and spare parts to manage.
- Educate Users – Train employees to spot exterior rust, bulges, or valve leaks and to tag suspect cylinders out of service immediately.
- Document Everything – File test certificates alongside OSHA or NFPA records; digital copies are acceptable but must be accessible during inspections.
Conclusion
Hydrostatic testing is more than a regulatory hurdle—it is a proven engineering safeguard that turns potential pressure bombs back into trustworthy tools. By subjecting each cylinder to stresses beyond everyday use, the process exposes hidden defects before they translate into deadly failures. Combine on-time testing with diligent documentation and operator training, and you create a safety culture that protects lives, property, and your organization’s reputation—under pressure and every day thereafter.
Source: Hydrostatic Testing: The Pressure-Proof Way to Guarantee Cylinder Safety